Industrial hydraulic cylinders
Industrial hydraulic actuators offer a number of advantages
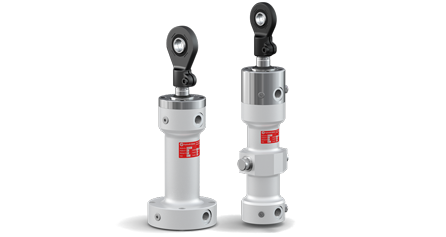
The requirements for hydraulic servo actuators and custom hydraulic cylinders vary depending on the ambient conditions in the place of application:
No matter under which conditions a hydraulic cylinder should work for you, we make it possible. With a complete system that is custom-made for your specifications and requirements.
Hänchen offers services that go far beyond the construction and manufacturing of an "high performance hydraulic cylinder":
Passion for high-quality hydraulic cylinders needs a basis of accuracy down to the last detail. Our cylinder production makes no compromises on quality, giving you every reason to choose Hänchen products:
80 % Vertical Integration.
100 % Made in Germany.
100 % Quality.
The high surface quality and geometrical accuracy of the component parts of every single Hänchen cylinder - standard or custom cylinders - guarantee a long life time without failure.
For the best lubrication and running properties and as little wear as possible on cylinders and seals, the cylinders' sliding surfaces are refined with a cross-hatch finish.
The constant development of our sealing systems - by combining already marketed and in-house developed seals - optimise all our hydraulic cylinders regarding wear, friction and leakage.
The guide clearance must be neither too small nor too large. This is why Hänchen places so much importance on optimal accuracy. The result is reduced stress on the guide and thus less wear on the component parts.
The fewer component parts a cylinder has, the less accident-prone it is. And the simpler and safer maintenance and installation is. The three main parts of a Hänchen hydraulic cylinder:
Our hydraulic cylinder pistons and piston rods are inseparably joined. The piston is coated with non-ferrous metal, enabling a precise metallic guide. The sophisticated rod ends with rounded edges permit a sealfriendly installation.
Round-head design, inseparably welded to the cylinder mounting. Drilled ports permit a space-saving installation with many options for adjustment to various applications.
A stick-slip-free cover type that is perfectly coordinated to the requirements is crucial for the service life of the entire hydraulic cylinder. Special feature: The synthetic guide is permanently integrated, reaches a better load distribution and minimises the risk of scratches caused by dirt particles.
Perfect combination: The cover type with the best sealing and guiding system* matching piston rod quality and the right sealing material is selected based on your application.
We'll tune your hydraulic cylinder. Tell us what you need – only
those who set conditions get the perfect industrial actuator.
SEALING SYSTEM | Basic design Lip seal, wiper ring |
Servocop® Compact seal, lip seal, wiper ring |
Servoseal® Servoseal®, lip seal, wiper ring |
Servofloat® Floating gap seal, functional oil seal, wiper ring |
Functional oil seal Functional oil seal, wiper ring |
GUIDING SYSTEM | ![]() |
![]() |
![]() |
![]() |
![]() |
![]() Servoslide®
Synthetic guide |
|
|
|
|
|
![]() Metallic
guide |
|
|
|
|
|
![]() PTFE-
Wear rings |
|
|
|
||
![]() Servobear®
Hydrostatic bearing |
|
Whether sensitive, free-moving or robust – extreme adaptability ist the strength of each Hänchen hydraulic cylinder and servo actuator.
We offer you always the best cover type with optimal friction force for static or dynamic applications.
Measured on double-rod cylinder (bore 46 mm without seal, rod Ø 40 mm) during sine operation according to VDMA 24577 at 50 °C/HLPD46.
The level of the friction force curves is lower than usual.
Beside the selected cover type, the right piston design is also crucial for the dynamic movement of hydraulic cylinders.
Equipping the rectangular compact seal with a static elastomer seal prevents lowering of the piston rod under load holding function of the cylinder for a longer period.
SEALING SYSTEM | Rectangular compact seal | Servoseal® | Throttle gap (without seal) |
GUIDING SYSTEM | ![]() |
![]() |
![]() |
Metallic guide |
|
|
|